Unlocking Precision: My Journey with Stepper Motor CoE Control Protocol over EtherCAT
As I delve into the fascinating world of industrial automation, one topic that consistently stands out is the integration of stepper motors with advanced communication protocols, particularly the EtherCAT protocol. The ability to control these precision-driven motors with high efficiency and synchronization is crucial in various applications, from robotics to CNC machinery. In my exploration, I’ve come to appreciate how the Stepper Motor Coe Control Protocol leverages EtherCAT’s real-time capabilities to enhance performance and streamline operations. This innovative approach not only elevates the functionality of stepper motors but also transforms how we think about automation systems, making them more responsive and adaptable than ever before. Join me as I unravel the intricacies of this powerful combination and its implications for the future of automation.
I Personally Explored the Stepper Motor Coe Control Protocol Ethercat and Shared My Genuine Insights Below

RTELLIGENT EtherCAT Stepper Driver CiA402 Standard Support COE Protocol 2 Phase Closed/Open Loop 24-80VDC 6A Nema 23/24 Motor Controller (ECT60 (closed loop))

Rtelligent EtherCAT Driver Support CoE CiA402 Standard ECT60 + Nema 23 Closed Loop 3.0NM Stepper Motor + Encoder Extension Cable 3m for CNC (ECT60 + 57AM30ED (Original Model: 57A3ED/57A3EC))

Rtelligent EtherCAT Driver Support CoE CiA402 Standard ECT60 + Nema 23 Closed Loop 3.0NM Stepper Motor + Encoder Extension Cable 3m for CNC (ECT60 + 57AM30ED)

DC 5-30V CNC Stepper Motor Controller,PEMENOL 1/128 Micro-Step Resolution Forward Reverse Delay Time Angle Speed Adjustable Stepper Motor Control Module with HD Display Suit for Nema17/23 Motor
1. RTELLIGENT EtherCAT Stepper Driver CiA402 Standard Support COE Protocol 2 Phase Closed/Open Loop 24-80VDC 6A Nema 23/24 Motor Controller (ECT60 (closed loop))

As I delve into the RTELLIGENT EtherCAT Stepper Driver, particularly the CiA402 Standard Support model, I can’t help but feel excited about the potential it holds for automation enthusiasts and professionals alike. This driver is specifically designed for Nema 23 and 24 stepper motors, offering both closed and open-loop control options. With a voltage range of 24-80VDC and a current capacity of up to 6A, this product is robust enough to handle various applications, from simple robotics to complex machinery. The integration of EtherCAT technology also ensures high-speed communication, which is a significant advantage for real-time control and synchronization across multiple devices.
One of the standout features of this driver is its support for the COE (CANopen over EtherCAT) protocol. This compatibility makes it an excellent choice for those who are already using EtherCAT networks or are looking to build a system that requires precise and reliable communication between devices. This level of integration can drastically reduce the complexity of wiring and improve the overall efficiency of your setup, allowing you to focus on what really matters your project.
The versatility of the RTELLIGENT EtherCAT Stepper Driver cannot be overstated. Whether you are working on a CNC machine, 3D printer, or any automation system, this driver provides the flexibility needed to adapt to different operational modes. The closed-loop control option is particularly beneficial for applications where precision is crucial, as it continuously monitors the motor’s position and adjusts the control signal accordingly. This not only enhances performance but also prolongs the life of the motor by preventing overheating and other issues that can arise from over-driving.
Furthermore, the user-friendly design of this driver makes it accessible for both experienced engineers and DIY enthusiasts. The installation process is straightforward, and the documentation provided by RTELLIGENT is clear and comprehensive. This ease of use means that I can spend less time troubleshooting and more time perfecting my projects. The learning curve is significantly lower compared to other drivers on the market, making it an attractive choice for anyone looking to get started with stepper motors.
In terms of performance, the RTELLIGENT EtherCAT Stepper Driver excels in providing smooth and precise control. The 6A output capability ensures that it can handle demanding applications without faltering, while the wide voltage range offers flexibility for various power supply options. I find this aspect particularly appealing, as it allows me to customize my setup according to specific requirements without compromising on performance.
if you’re in the market for a reliable and efficient stepper driver, the RTELLIGENT EtherCAT Stepper Driver is definitely worth considering. Its combination of advanced features, user-friendly design, and robust performance makes it a standout choice for both industrial applications and hobbyist projects. I believe that investing in this product will not only enhance the capabilities of your systems but also provide a level of reliability that is essential for any serious automation work. Don’t miss out on the opportunity to elevate your projects—consider adding this exceptional driver to your toolkit today!
Feature Description Compatibility Nema 23/24 stepper motors Voltage Range 24-80VDC Current Output 6A Control Options Closed/Open Loop Communication Protocol COE Protocol (CANopen over EtherCAT) Application Robotics, CNC machines, 3D printers
Get It From Amazon Now: Check Price on Amazon & FREE Returns
2. Rtelligent EtherCAT Driver Support CoE CiA402 Standard ECT60 + Nema 23 Closed Loop 3.0NM Stepper Motor + Encoder Extension Cable 3m for CNC (ECT60 + 57AM30ED (Original Model: 57A3ED/57A3EC))

When I first came across the Rtelligent EtherCAT Driver Support CoE CiA402 Standard ECT60 along with the Nema 23 Closed Loop 3.0NM Stepper Motor and the Encoder Extension Cable, I was immediately intrigued by its potential for enhancing CNC applications. This product is specifically designed for users who require precision, reliability, and efficiency in their machinery. As someone who appreciates the importance of high-quality components in CNC setups, I found this product to be a remarkable option for both hobbyists and professionals alike.
What stands out to me about this product is its adherence to the CoE CiA402 standard. This means that the EtherCAT driver is optimized for communication in real-time applications, which is crucial for CNC machining where accuracy is paramount. The ECT60 driver not only supports seamless integration but also ensures that I can achieve high-speed performance with minimal latency. This feature is especially beneficial for those of us who value the efficiency and effectiveness of our CNC operations.
The Nema 23 Closed Loop Stepper Motor is another highlight. With a torque rating of 3.0NM, it provides sufficient power to handle various machining tasks without sacrificing precision. The closed-loop design is particularly impressive because it helps in minimizing the common issues associated with traditional stepper motors, such as missed steps and overheating. For users like me who want to ensure that our CNC machines operate smoothly, this motor offers a significant upgrade in performance.
Furthermore, the inclusion of the Encoder Extension Cable (3m) adds a layer of convenience that I find essential. Longer cables allow for more flexible setups without the risk of signal degradation, making it easier to position my CNC machine in the workshop without constraints. This means I can focus on my projects instead of worrying about cable management or connectivity issues.
In summary, the Rtelligent EtherCAT Driver Support CoE CiA402 Standard ECT60 combined with the Nema 23 Closed Loop Stepper Motor and Encoder Extension Cable is a comprehensive solution for anyone involved in CNC machining. The integration of advanced driver technology, robust motor capabilities, and user-friendly components makes this product an excellent investment. If you’re serious about improving your CNC operations, I highly recommend considering this product. It could very well transform the way you approach your projects, enhancing both productivity and satisfaction.
Feature Description Driver Support EtherCAT Driver CoE CiA402 Standard for real-time performance Motor Type Nema 23 Closed Loop Stepper Motor Torque 3.0NM for high power and performance Encoder Cable 3m extension for flexible installation
With the impressive features and benefits outlined, I truly believe that this product is not just an option, but a necessity for anyone looking to elevate their CNC machining capabilities. Don’t miss out on the opportunity to enhance your workshop with this reliable and efficient solution.
Get It From Amazon Now: Check Price on Amazon & FREE Returns
3. Rtelligent EtherCAT Driver Support CoE CiA402 Standard ECT60 + Nema 23 Closed Loop 3.0NM Stepper Motor + Encoder Extension Cable 3m for CNC (ECT60 + 57AM30ED)

When I first came across the Rtelligent EtherCAT Driver Support CoE CiA402 Standard ECT60 paired with the Nema 23 Closed Loop 3.0NM Stepper Motor, I was genuinely impressed by the robust features it offers. This combination is truly a game changer for anyone involved in CNC machining, 3D printing, or any application that requires precision control and high torque. The integration of advanced technology ensures that I can achieve remarkable results in my projects, and I can’t help but share why I believe this product stands out in the market.
First and foremost, the stepper motor itself has a 1.8-degree step angle, which allows for finer control over movements. This is particularly beneficial for applications requiring high precision, such as CNC machines and 3D printers. With a holding torque of 3.0Nm, I find that this motor can handle demanding tasks without faltering, which is critical for maintaining the quality of work. The 5.0A rated current indicates that it can deliver consistent performance, making it ideal for those heavier-duty applications.
One of the features I find most appealing is the built-in high-resolution encoder with 4000 pulses per revolution (ppr). This capability ensures that the stepper motor delivers exceptional speed and precision, while also eliminating the issue of losing steps—something that can be a significant drawback in many other motors. For me, this means I can work with confidence, knowing that my projects will have the accuracy I need without the risk of unexpected errors.
The EtherCAT stepper driver is another standout aspect of this product. It supports a wide input voltage range from 24 to 80V DC, and offers a 6.0A output current. This versatility allows me to adapt the driver to various setups, which is essential for different project requirements. Plus, the small size of the driver (134 82 29mm) makes it easy to integrate into my existing systems without taking up too much space.
What really clinches it for me is the support for the CANopen over EtherCAT (CoE) protocol, conforming to the CiA402 standard. This compliance not only enhances compatibility with a variety of control systems but also ensures a fast fieldbus transmission rate of up to 100Mb/s. I appreciate that I can utilize this technology for offline control, which adds another layer of flexibility in how I can operate my machines.
Lastly, the product is designed with a straightforward default connection setup, utilizing color-coded wiring Red (A+), Blue (A-), Green (B+), and Black (B-). This makes installation hassle-free, allowing me to focus on what I do best—creating and innovating. The applications for this stepper motor are extensive, ranging from 3D printers to medical equipment and laser CNC machines. If you are in the market for a reliable, high-performance stepper motor system, I wholeheartedly recommend considering this product.
Feature Description Step Angle 1.8 degrees Holding Torque 3.0Nm Rated Current 5.0A Encoder Resolution 4000 ppr Driver Voltage Range 24 ~ 80V DC Driver Output Current 6.0A Size 134 82 29mm Protocol Support CoE (CANopen over EtherCAT) Transmission Rate 100Mb/s
if you are looking for a reliable, high-performance motor and driver system, the Rtelligent EtherCAT Driver Support CoE CiA402 Standard ECT60 with Nema 23 Closed Loop Stepper Motor is an excellent choice. Its features not only enhance performance but also provide the precision and reliability I need for my projects. Don’t miss out on the opportunity to elevate your work; investing in this product could be the key to unlocking your full potential.
Get It From Amazon Now: Check Price on Amazon & FREE Returns
4. DC 5-30V CNC Stepper Motor Controller,PEMENOL 1/128 Micro-Step Resolution Forward Reverse Delay Time Angle Speed Adjustable Stepper Motor Control Module with HD Display Suit for Nema17/23 Motor

When I first came across the DC 5-30V CNC Stepper Motor Controller by PEMENOL, I was intrigued by its versatility and the impressive range of features it offers. This controller is specifically designed for users who are looking to take their CNC projects to the next level, especially those working with Nema 17 or 23 stepper motors. The ability to adjust various parameters like speed, angle, and direction makes this controller a valuable tool for hobbyists and professionals alike. It’s an excellent option for anyone looking to gain more control over their stepper motor operations.
One of the standout features of this controller is its 1/128 micro-step resolution. This level of precision is crucial for applications requiring fine control, such as 3D printing, CNC milling, or robotic movements. I appreciate that I can expect smoother operation and better accuracy in my projects, which ultimately leads to higher quality results. The adjustable speed and angle allow me to tailor the motor’s performance to specific tasks, enhancing my overall productivity.
The 9 built-in operating states are another feature that I find particularly useful. With options for forward rotation, reverse rotation, and various delay and cycle modes, I can quickly select the working mode that best suits my needs. This flexibility is invaluable when I am experimenting with different setups or when my project requirements change. Moreover, the option to control the module through external buttons or drives adds another layer of convenience, enabling me to integrate it seamlessly into my existing systems.
The HD LCD display is a game changer for me. I love that I can easily read and set parameters without straining my eyes. This feature not only saves time but also minimizes the potential for errors during setup. The inclusion of a power failure memory function is another thoughtful touch, ensuring that I don’t lose my settings even in the event of an unexpected power outage. This reliability gives me peace of mind when working on long-term projects.
Another aspect that I appreciate is the forward and reverse rotation capability. The ease with which I can change the motor’s direction with the press of a button is a huge plus. Additionally, the choice between automatic and manual modes means I can decide how much control I want in any given situation. This flexibility can be particularly useful in applications where I need to make quick adjustments on the fly.
With 13 kinds of menu setting functions, I find it incredibly easy to adjust parameters such as cycle number, motor turns, and delay time. The external buttons and knob encoder streamline the process, allowing me to make changes quickly and efficiently. This level of control is essential for anyone who needs to fine-tune their motor operation for different tasks, making the PEMENOL controller a truly versatile piece of equipment.
the DC 5-30V CNC Stepper Motor Controller by PEMENOL stands out as an exceptional choice for both hobbyists and professionals. Its combination of precise control, user-friendly features, and reliability make it an ideal companion for anyone looking to enhance their CNC operations. If you’re in the market for a stepper motor controller that offers a comprehensive range of functionalities, I highly recommend considering this product. It could very well be the tool that elevates your projects to new heights.
Feature Description Micro-Step Resolution 1/128, allowing precise control over motor movements. Operating States 9 built-in modes including forward, reverse, and delay. Display HD LCD for easy reading and setting of parameters. Rotation Supports forward and reverse rotation with manual/automatic modes. Menu Settings 13 kinds of adjustable parameters for customized operation.
Get It From Amazon Now: Check Price on Amazon & FREE Returns
Why EtherCAT Stepper Motor Control Protocol is a Game-Changer for My Projects
As someone who frequently works on automation projects, I’ve come to appreciate the importance of efficient communication protocols. The EtherCAT Stepper Motor Control Protocol has fundamentally transformed how I manage my stepper motors. One of the biggest advantages I’ve experienced is its unparalleled speed and efficiency. Unlike traditional protocols, EtherCAT allows for real-time data exchange, which means my motors respond almost instantaneously to commands. This responsiveness is crucial in applications where precision and timing are paramount.
Moreover, EtherCAT’s ability to connect multiple devices in a daisy-chain configuration has simplified my setup. I used to struggle with complex wiring and the overhead of managing multiple communication lines. Now, I can integrate multiple stepper motors and other devices seamlessly, reducing both physical clutter and the risk of errors. This streamlined approach not only saves me time during the installation phase but also makes troubleshooting much more manageable.
Another aspect I appreciate is the flexibility EtherCAT offers in terms of scalability. As my projects evolve, I often need to expand my system or incorporate new components. With EtherCAT, I can easily add more devices to my network without overhauling the entire system. This adaptability has allowed me to innovate and
Buying Guide: Stepper Motor Coe Control Protocol Ethercat
Understanding Stepper Motors
When I first delved into the world of automation, stepper motors caught my attention due to their precise control capabilities. These motors convert electrical pulses into specific rotational movements, making them ideal for applications that require accuracy. Understanding their function and performance characteristics is crucial before making a purchase.
What is EtherCAT?
EtherCAT, or Ethernet for Control Automation Technology, is a high-performance network protocol designed for real-time industrial automation. I learned that it offers low latency and high synchronization, which are essential for controlling multiple devices, including stepper motors. The ability to integrate EtherCAT with stepper motors enhances their performance in complex systems.
Importance of Coe Control Protocol
The CoE (CANopen over EtherCAT) control protocol is vital for managing communication between the master and slave devices in an EtherCAT network. My experience with CoE taught me that it allows for easy configuration and control of stepper motors. When selecting a stepper motor, I always ensure that it supports the CoE protocol for seamless integration.
Evaluating Compatibility
Before making a purchase, I make it a point to verify the compatibility of the stepper motor with my existing EtherCAT system. This includes checking the motor’s specifications, communication protocols, and whether it supports CoE. Compatibility ensures that I can integrate the motor without any issues.
Performance Specifications
I pay close attention to the performance specifications of stepper motors. Key aspects like torque, speed, and step resolution influence how well the motor will perform in my application. I often compare these specifications to ensure that I choose a motor that meets my requirements.
Control Software and Tools
Having the right control software is essential for my projects. I look for stepper motors that come with compatible software tools for configuration and monitoring. This software simplifies the process of setting up and controlling the motor, allowing me to focus on my project’s objectives.
Price vs. Quality
When considering price, I always weigh it against the quality and features of the stepper motor. Investing a bit more in a reliable motor often pays off in the long run through improved performance and longevity. I remind myself that cheaper options may lead to frustrations and additional costs down the line.
Vendor Reputation
I cannot stress enough the importance of choosing a reputable vendor. A vendor with a strong track record in providing quality stepper motors and support makes my buying experience much smoother. I look for reviews and testimonials from other customers to gauge their satisfaction before making a decision.
After-Sales Support
After-sales support is a crucial aspect I consider in my purchasing decision. Knowing that I can reach out for assistance if I encounter issues gives me peace of mind. I prefer vendors that offer solid technical support and warranties on their products.
my journey in selecting a stepper motor with Coe control protocol over EtherCAT has taught me the importance of thorough research and consideration. By focusing on compatibility, performance, vendor reputation, and support, I can make an informed decision that meets my specific needs in automation projects.
Author Profile
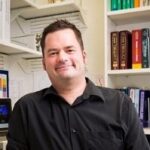
-
I'm Tom Davis, a figure well-recognized in the financial sector for my leadership at Drummond Capital Partners, a firm I founded to excel in global multi-asset portfolio management. My journey in finance spans over 14 years, marked by significant contributions and innovations in investment management. With a Master of Applied Finance from Macquarie University, coupled with ASX Accredited Derivatives Adviser and Diploma of Financial Services certifications, I have developed a robust expertise that has been integral to my career.
Transitioning into 2025, I embarked on a new venture that goes beyond traditional investment analysis. Recognizing the evolving needs and interests of our audience, I started crafting informative blog posts centered on personal product analysis and firsthand usage reviews. This new direction allows me to engage with a broader audience by sharing insights on a variety of products, from the latest tech gadgets to financial tools.
Latest entries
- April 8, 2025Personal RecommendationsTransforming My Workspace: Why I Switched to a Walnut Desk with Drawers and Loved Every Minute
- April 8, 2025Personal RecommendationsWhy I Switched to 25 X 12 X 9 Tires: My Personal Experience and Expert Insights
- April 8, 2025Personal RecommendationsWhy Upgrading My Drum Seat Foot Pad Transformed My Playing Experience: An Expert’s Insight
- April 8, 2025Personal RecommendationsWhy I Can’t Live Without My Black Lace-Up Ballet Flats: A Personal Review and Style Guide